FREQUENTLY ASKED
QUESTIONS
Have questions? We've got answers. If our product search or product pages didn't help you find what you were looking for, check here for some frequently asked questions and answers.
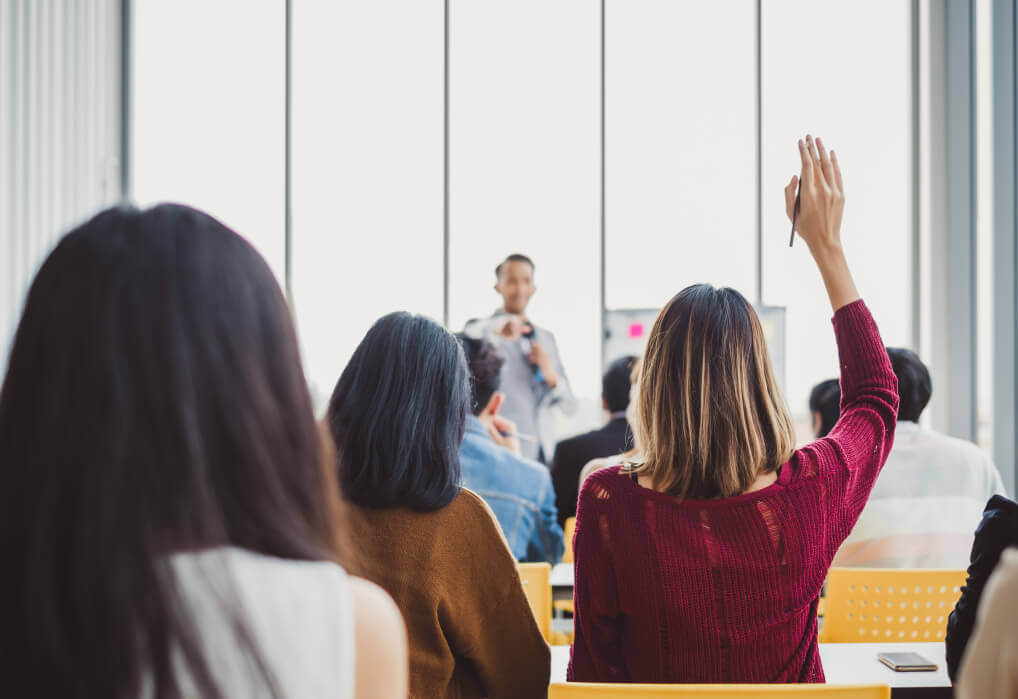
Our mission is to be a global market leader in life science and medical microscopy products with the highest price-to-performance ratio. Our microscopes must serve to enhance research and medical diagnostics. The principal elements of our strategy are:
- Meticulous attention to the industrial concept of any product, ensuring all customer needs are reflected through product innovations.
- Careful synchronization of design, engineering, and production processes to ensure that our vision of flawless functionality is realized from beginning to end.
- Thoughtful execution of quality control and product support to our network of faithful distributors so that our customers realize the supreme value in owning a Labomed microscope.
There are six disciplines we adhere to produce superior optics:
- Design
- Optical component production
- Optical component testing
- Assembly
- Alignments
- Repeatability
Barring the top 4 microscope manufacturers (Zeiss, Leica, Olympus, and Nikon), most if not all microscope manufacturing companies do not invest in their optical design. They usually repackage an existing design available off-the-shelf from a Chinese supplier. Such designs are based on old-generation systems. Modern design software. have the immense power to calculate performance aberrations across millions of surface points on optical surfaces. Glass types used in these systems also tend to be antiquated.
There are companies producing designs calculated by inexperienced designers. A good designer must have had the experience of seeing multiple systems created by him in actual production to understand that what works in practice can be quite different from theory.
With over 70+ years in business, our group’s core strength is specialized skilled, and experienced designers equipped with the absolute latest design and most advanced engineering tools to aid in producing practical, workable, efficient, and innovative solutions considering all design constraints like realistic lens element centers and edge thicknesses, minimum and maximum air-spaces between lenses, maximum constraints on entrance and exit angles, physically realizable glass index of refraction and dispersion properties in achieving excellence through a mix of experience and technology. Also, with state-of-the-art optical production lines, we can include complex visual forms and tolerances in our designs that significantly contribute to superb optical performance. Lastly, we have designed and implemented our property coating technology, MaxLite, which helps us maintain 97% of light transmission from the source and yields the best anti-scratch, anti-fog, and anti-reflection properties in the class.
When a design originates from a brand and is produced in its facilities, it goes through at least two rounds of iterations. Besides the top four brands, Labomed® is one of the few with its top-of-the-line optical production technologies. Everything is done in-house in close collaboration with design and production departments, from design to prototyping to designing iterations and final products. 2. Because of the ability to produce these components in-house, we can keep very tight quality control on the fit, form, and cosmetics, including surface flatness, finishing power, and irregularities of optical parts throughout the production and postproduction processes.
Also, with in-house facilities such as interferometers, multilayer optical coating systems, coordinate measuring machines, spectrophotometers, we can control critical parameters of optical components that contribute to the high performance of optical modules.
Our adapted quality culture complies with USFDA 21 CFR part 820 and ISO 13485, meaning strict implementation and process control discipline, lean manufacturing tools including 5S and kaizen, from sourcing of material through to final product release.
An essential requirement of optical modules is the repeatability of their performance at all magnifications and easy interchangeability. It is most necessary for upgrades and field replacements to avoid product recalls and breakdowns requiring complex repairs and servicing.
In optical manufacturing, technology alone is not enough without the skill and experience to achieve supreme excellence in quality. Continuous training and sustainable employment are essential facets of our quality culture.
A great contributor to the final optical performance is the assembly process of the optics to their host mechanical parts. Exceptional tools, alignment jigs, fixtures, collimators, and test charts are required to ensure performance as per desired specifications. Clear-eyed on these facts, we employ world-class systems and systems unique to our design to ensure zero errors of a tip, tilt, wedge, image run-outs, or re-introduction errors that significantly contribute to the performance of our overall optical system. We pay special attention to quality during part handling and cleaning. Ultrasonic cleaning and clean air benches are part of standard assembly protocols to achieve the best-finished product quality.
All electrical components are supplied by UL-approved manufacturers. Our final power supplies are designed and developed in-house to maintain the highest degree of control on what leaves our factory doors. Our 50W LED systems in our surgical modules are some of the best in class, yielding more than 125k Lux in Prima and 90k Lux in Magna in one of the quietest and most compact form factors available. Shelf life is more than 50K hours.
All electrical components are supplied by UL-approved manufacturers. Our final power supplies are designed and developed in-house to maintain the highest degree of control on what leaves our factory doors. Our 50W LED systems in our surgical modules are some of the best in class, yielding more than 125k Lux in Prima and 90k Lux in Magna in one of the quietest and most compact form factors available. Shelf life is more than 50K hours.
The Labomed brand is manufactured in a large global supply chain. With facilities in California (USA), Rotterdam (The Netherlands), and New Delhi (India). As a group, we are strategically located to source the best input components and materials while keeping our costs in check, helping us pass the savings on to our clients in the form of an excellent product at hard-to-beat prices. Labomed Group operates four independent factories in India as well as one manufacturing base in California. All our products are designed, developed, and controlled by our highly experienced team of engineers at Labo America, Inc., USA.
All of our facilities are ISO 9001. All medical manufacturing facilities are ISO 13485. All products hold UL and CE certifications.
Our medical products offer two years for parts, labor, and cameras and one year for electrical aspects (lifetime in North & South America). Our life sciences products provide five years for parts and labor, two years for cameras, and one year for electrical components.